一、传统工时管理为何总是“漏洞百出”?
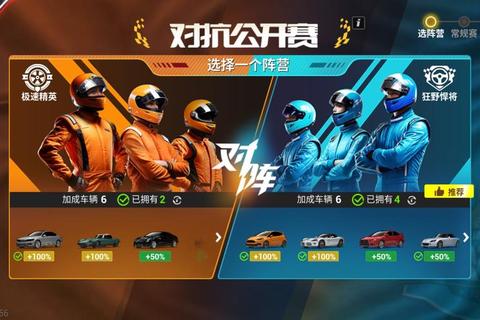
制造业财务总监张磊最近陷入困惑:公司年度审计时发现,手工统计的工时数据与实际产能相差18%,直接导致300万元成本核算偏差。这种场景在2025年的今天仍非个例,中国中小企业协会数据显示,73%的企业存在工时记录失真问题,每年因此损失超千亿。当纸质表格遇上多班倒作业,当Excel公式撞上跨部门协作,传统工时管理就像漏水的木桶,永远装不满效率的清泉。
这正是“高效能极速版工时软件智能追踪时间助力效能飞跃巅峰”诞生的时代背景。这类软件如同给企业装上CT扫描仪,不仅透视每个生产环节的真实耗时,更通过AI算法重构效能坐标系。某汽车零部件厂引入该类系统后,成功将模具切换时间从47分钟压缩至19分钟,相当于每年多产出2.4万套产品。
二、智能追踪如何破解工时“黑洞”?
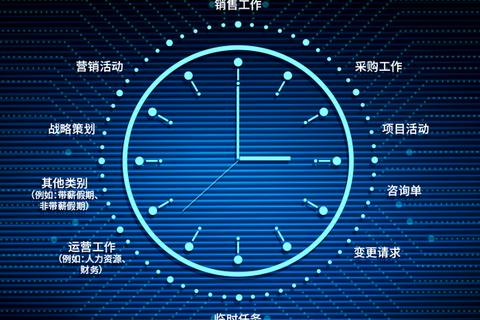
重庆某摩托车制造厂的案例颇具说服力。该厂过去采用纸质工单,机加工车间每天产生2000多张记录单,月底总有15%的工时数据无法对应。引入极速版工时软件的RFID工位感应系统后,每个工序的启停时间精确到秒,系统自动生成《异常工时分析图谱》,仅用3个月就将计划达成率从82%提升至95%。
这套系统的核心在于三重穿透:
1. 设备级穿透:通过物联网传感器捕获机床实际运转时长,区分设备空转与有效加工时间。某注塑车间因此发现32%的能耗浪费在设备待机上。
2. 操作级穿透:结合动作捕捉技术,智能分解装配工序。某家电企业发现螺丝紧固动作平均耗时超标26%,经动作优化后单台装机效率提升19%。
3. 流程级穿透:自动绘制价值流图,暴露工序衔接中的隐形损耗。某食品包装线通过消除3处冗余搬运,使日产能突破设计极限12%。
三、数据沉淀怎样转化为决策智慧?
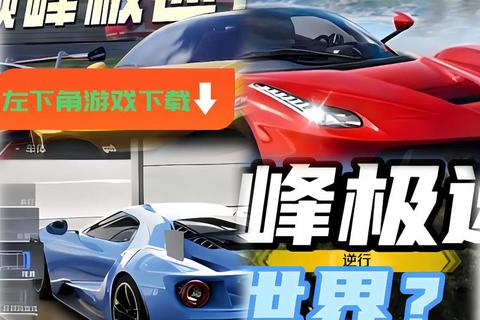
广东某LED照明企业的数字化转型颇具启示。其使用的极速版系统具备“数据酿酒”功能——将三年工时数据导入AI模型后,自动生成《柔性排产决策树》。当北美客户临时加单20万件时,系统10分钟内完成144台设备、500名工人的最优排程,交货周期反而缩短3天。
这种智能决策依托三大数据引擎:
效能基准引擎:建立2000多个工艺参数的动态标准库,青岛某船舶配件厂的焊接工时标准差从±18%降至±5%。
风险预警引擎:深圳电子厂通过实时比对3000个工单数据,提前48小时预警产能缺口,避免百万级订单违约。
持续改进引擎:杭州某数控车间利用软件生成的《月度效能波动热力图》,锁定7个工艺改进点,年节省直接人工成本270万元。
四、效能革命需要怎样的新基建?
北京某航天精密制造企业的实践揭示了关键路径。该企业部署“高效能极速版工时软件智能追踪时间助力效能飞跃巅峰”系统时,同步实施三项变革:
1. 组织再造:设立由IE工程师、数据架构师组成的数字化办公室,每周解读系统生成的《价值流失TOP10清单》。
2. 规则重构:将软件采集的368项效能指标纳入KPI体系,车间主任奖金与设备综合效率(OEE)直接挂钩。
3. 文化重塑:开发员工端的“效能数字孪生”APP,工人可实时查看个人效能排名及改进建议,激发全员改善热情。
这场革命需要警惕三个误区:
避免将软件视为“电子监工”,成都某机械厂因此流失12%的技术骨干,后改为“改善积分奖励制”才扭转局面。
防止数据孤岛,建议选择能对接ERP、MES的开放式系统,如某新能源车企通过API接口实现全价值链数据贯通。
拒绝静态标准,杭州某智能仓库的软件每月自动更新拣货工时基准,始终保持与设备升级同步。
对于准备启程的企业,建议实施“三步走”策略:
1. 诊断阶段:用免费试用版完成车间级数据采集(推荐Zoho Projects或8Manage的基础版)。
2. 试点阶段:选择1-2条产线进行3个月深度验证,重点观察异常工时处理效率。
3. 推广阶段:构建包含IT、生产、HR的跨部门推进组,配套修订18项管理制度。
当“高效能极速版工时软件智能追踪时间助力效能飞跃巅峰”真正融入制造基因,企业收获的不仅是数字面板上的效率提升,更将建立起面向智能时代的核心竞争力。正如海尔某互联工厂的车间标语所示:“看不见的分钟,看得见的未来”。