传统制造业的困局:数字化仿真能否破解效率与成本之痛?
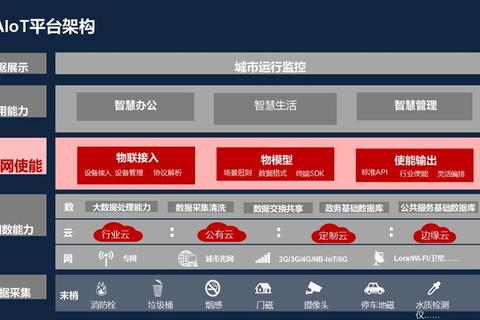
在汽车工厂里,工程师们正为一条新建产线的调试焦头烂额——价值千万的设备因布局不合理导致物流堵塞,实际产能仅为设计值的60%。这种场景每天都在全球制造业上演,据麦肯锡研究显示,传统制造企业因规划失误造成的经济损失高达年度营收的5%-8%。面对日益复杂的生产系统,高效智能数字化工厂仿真软件驱动智造革新新纪元正在颠覆这一局面,但质疑声随之而来:虚拟世界的模拟结果真能指导现实生产吗?
一、如何让生产系统「先试后建」?
在北京某新能源汽车电池工厂的案例中,工程师运用达索系统DELMIA搭建三维虚拟车间,仅用72小时就发现原方案存在12处设备干涉点,优化后节约改造成本3800万元。这种「数字沙盘」技术已形成完整方法论:
1. 全要素建模:Visual Components提供的2000+标准化设备模型库,支持从传送带到工业机器人的快速布局
2. 动态推演:某钢铁企业通过AnyLogic模拟原料输送系统,精准预测设备利用率波动区间,将采购成本降低17%
3. 智能预警:海克斯康数字孪生平台提前9个月发现某变速箱产线振动超标,避免3000万元质量事故
这些实践印证了高效智能数字化工厂仿真软件驱动智造革新新纪元的底层逻辑:用数据流重构物理世界的因果链。
二、技术融合如何催生「柔性制造」?
当个性化定制需求冲击传统产线时,北京欧倍尔的解决方案给出答案。某家电企业通过「智慧桌面工厂」微缩模型,实现从大规模生产到C2M模式的切换:
基于MR混合现实技术,操作员可实时查看不同产品规格的装配指引
动态工艺算法在10分钟内生成36种排产方案,设备切换时间缩短至15分钟
数字孪生系统同步追踪138个质量参数,使定制产品良率从82%提升至95%
这种虚实交融的模式正重构生产范式。据IDC数据,采用仿真驱动的柔性工厂,订单响应速度提升40%,库存周转率提高2.1倍。
三、人才培育怎样跨越「虚实鸿沟」?
唐山某职业院校的变革颇具启示:通过「可拆卸微型工厂」实训系统,学生能在桌面完成整车厂级别的工艺验证。这套由智能机电模型与云仿真平台组成的教学系统:
支持22种工业通信协议的真实设备交互
内置300+典型故障案例库,覆盖85%的现场问题
动态评分系统精确量化操作熟练度,培训周期缩短60%
这种教育革新正在弥合产业人才缺口。教育部《智能制造人才白皮书》显示,掌握仿真技术的工程师薪酬溢价达34%,岗位需求年增长率持续保持在25%以上。
面对智造转型浪潮,企业可采取三步走策略:
1. 诊断先行:参照Gartner技术成熟度曲线,评估现有系统的数字化瓶颈
2. 场景切入:优先在工艺设计、设备运维等价值密度高的环节部署仿真模块
3. 生态共建:联合高校建设「数字工匠」培养体系,如华为与清华共建的工业互联网实验室
高效智能数字化工厂仿真软件驱动智造革新新纪元不是未来时,而是进行时。当某光伏企业用虚拟调试将新品上市周期压缩至28天时,这个答案已然清晰——在数字与现实的交响中,制造业正谱写新的效率史诗。